Manufacturing at Yamato
At Yamato Gokin, we manufacture both bulk orders and small-quantity orders. For bulk orders, we manufacture our special copper alloys into forgings, rolled plates, extruded bars and pipes, drawn bars, sand castings, and die castings. Smaller-quantity orders can be placed for our precision casting and pressure casting molds.
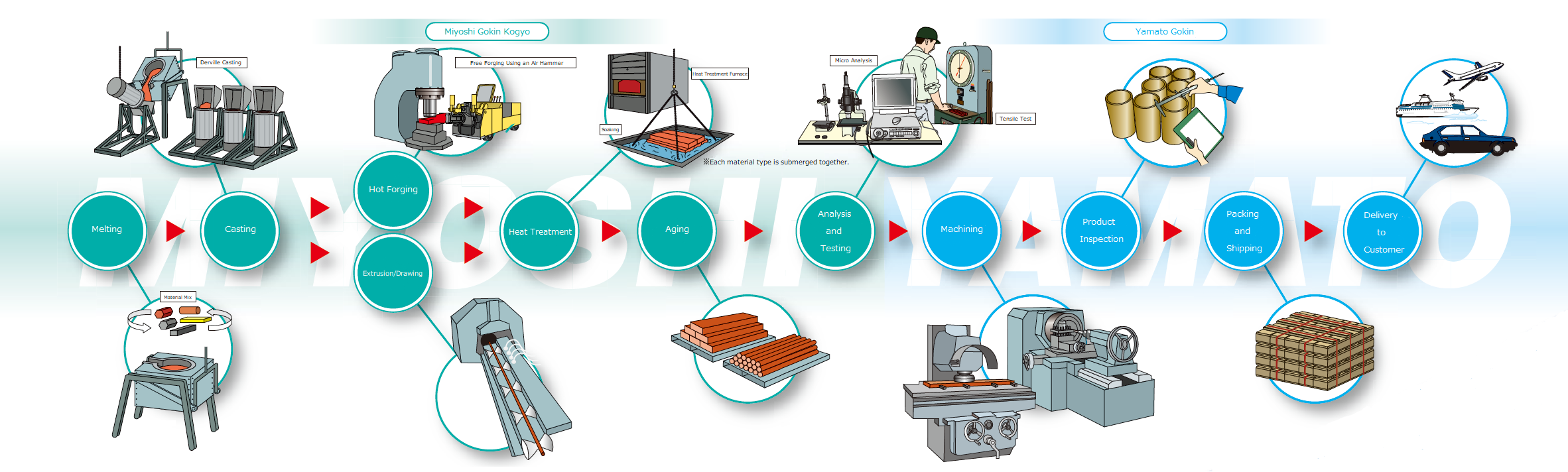
Melting and Casting
We melt and cast our copper alloys to make aluminum bronze, beryllium copper, copper chromium, high strength brass, and our NC (Corson System).
Hot Forging
Hot forging is a metalworking process in which metal, known as a billet, is shaped by exerting pressure through hammering or pressing. After its initial casting and cooling and before forging, the billet is heated to about 75% of its melting temperature to begin shaping the metal into the shape desired by the customer.
Extrusion or Drawing
In addition to hot forging, our material can be extruded or drawn into bars, pipes, and cylinders.
Extrusion
To extrude our materials at the billet stage, we reheat the metal at a temperature below melting and run the softened metal through a die (shaping mold) in our extrusion machine.
Drawing
We form cylinders from our metal material by drawing or pulling reheated and softened metal billet through a die or shaping mold that is set into our drawing machine.
Heat Treatment and Aging
To create metal alloys that suit our customers’ specific needs, we also offer heat treatment. Our heat treatment process includes reheating the forged or shaped metal in our furnace at a temperature below melting. After heating, the treated metal it is quickly cooled in a bath of water for a time specific to the material’s specifications in an aging process.
This heat treatment and aging process alters the microstructure of the metal and allows for heightened strength and hardness and a decrease and ductility in the alloy.
Analysis and Testing
As our material is going through the shaping and conditioning process, we take a small sample of the material for testing.
Using a material sample, we analyze the chemical composition of the alloy, and we conduct hardness, tensile, ultrasonic (UT), and penetrant (PT) tests to ensure that it meets applicable specification standards.
Machining
Once the alloy material has passed all tests, we proceed to machining of the metal as requested by the customer. During this stage, the alloy is cut into its final shape and polished.
Product Inspection
Before packing, shipping and delivery to the customer, we conduct a final inspection of the finished product.
Packing and Shipping
Once our product has been inspected, we prepare it in-house for shipping and delivery to the customer.
To inquire about our manufacturing process, or to place an order, please visit our contact page.

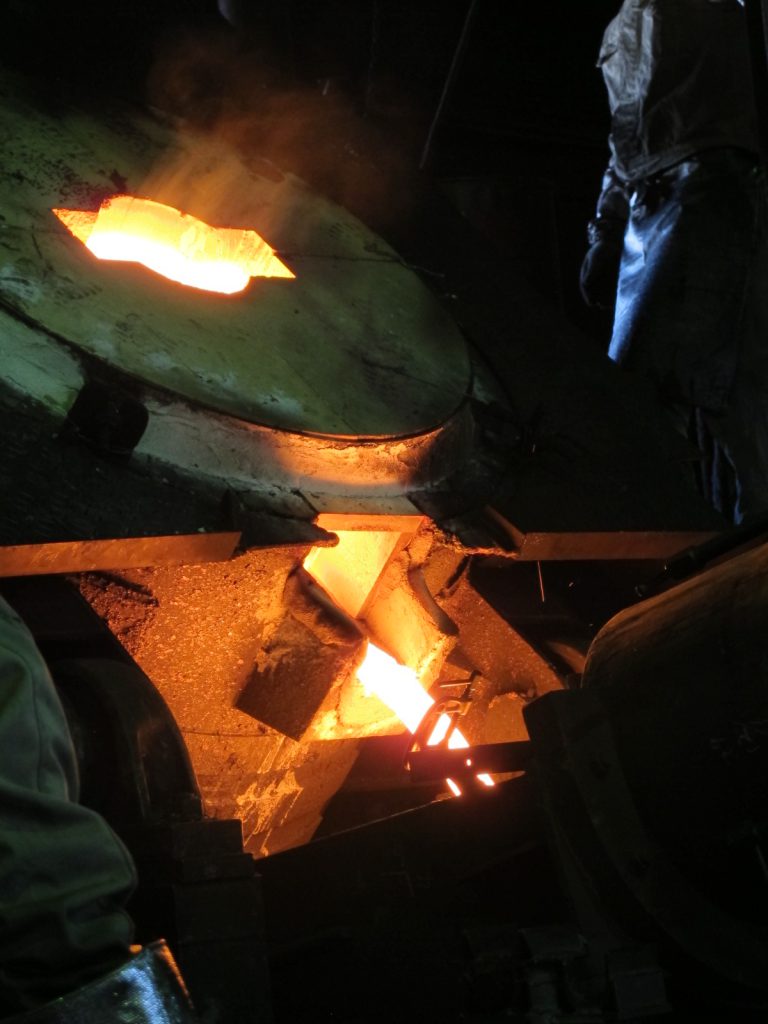
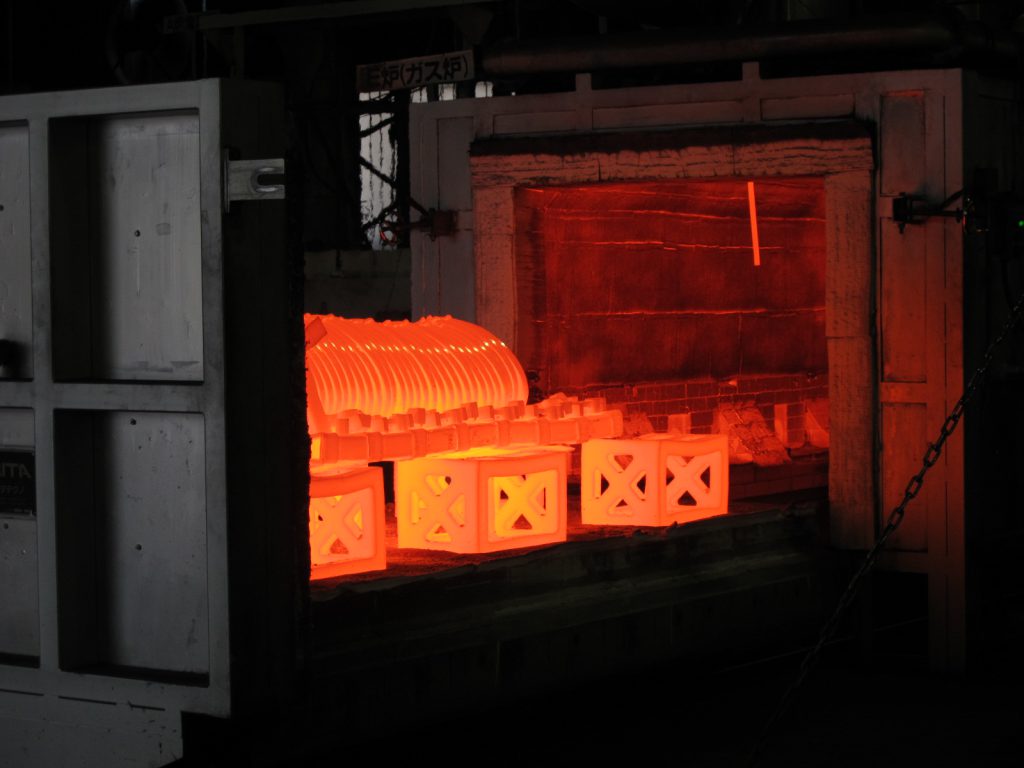